How To Repair Your Fridge - Quickly and Cheaply! (Fix It Yourself Series)
Author: David Roster
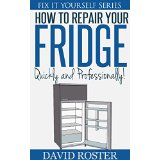
Book Series: How To Repair Your
Introduction
A refrigerator is one of the few appliances in the home that runs 24 hours a day 7 days a week. Owners don’t turn their refrigerators off at night to save energy. There’s usually food inside that’s dependent on the refrigerator for freshness.
A refrigerator is designed to work hard and long. While some modern refrigerators may have a lot of bells and whistles on the doors, the internal components of most refrigerators is nearly the same. The inside of the refrigerator is designed to operate off only a few simple components.
Refrigerators don’t break down often. After all, they are designed with durability, sustainability, and efficiency in mind. If they do break down, the owner always has the option of paying the bill for a professional repairman to fix the problem.
Professional refrigerator repairs are never cheap. Many of the repairs could be performed by the owner with ease if they only understood the appliance, how to troubleshoot, and how to make the actual repairs. With the exception of a few rare problems, most repairs on a refrigerator can be handled quickly and cheaply at home.
The important parts of the refrigerator include the coils, the compressor, the expansion valve, refrigerant, capacitors, and the heat-exchanging pipes. If there are electronics on the front door, then there’s also internal circuitry converting the electricity to the proper DC voltage and then operating the circuitry.
The difference between the person who spends a lot of money on the professional and the person who fixes their own refrigerator quickly and cheaply is usually a lack of understanding. A refrigerator may seem like a large, complex, and mysterious machine, but once you actually learn how it works you may realize it doesn’t take much to troubleshoot and repair one.
Learning to properly troubleshoot is just as important as knowing how to make the actual repairs, as it goes with any appliance. Those who can’t troubleshoot can’t really know if they are fixing the right problem. Luckily, the simplicity of the refrigerator makes it easy to troubleshoot and diagnose common problems.
The following section is the first step towards gaining the understanding required to approach a malfunctioning refrigerator with confidence. Next is the history of the modern refrigerator as well as an explanation of how the refrigerator actually operates.
A Brief History of the Refrigerator
Believe it or not, there was a time before the refrigerator. Prior to the development of refrigeration technology, people typically relied on icehouses as the only source of long-term cold storage. An icehouse is simply a small building designed to store ice throughout the year. These were most often built near sources of natural ice.
Ice was then kept cool using insulating it with materials like sawdust or straw. Once winter was upon them, the people could keep beverages cool just by keeping them outside. It wasn’t until 1755 that William Cullen designed a refrigeration machine and changed the world.
The process was remarkably similar to the modern refrigerator in many ways. A small pump was worked to create a vacuum directly above a container with diethyl ether inside. The ether would then begin boiling and absorb much of the surrounding heat from the air.
This 18th century refrigeration device was even used to create a small amount of ice. Unfortunately, the design was not perfected enough and it saw no real practical use at the time. From there, it was a series of experiments that led to the creation of the modern refrigerator.
19th century research into refrigeration began with Oliver Evans. He described an idea for a closed vapor-compression refrigeration mechanism. He wanted his idea to be used as a new source of ice, thus removing the country’s reliance on ice found in nature. His idea also utilized a supply of ether trapped beneath a vacuum.
Later, in 1820, a British scientist by the name of Michael Faraday perfected techniques for liquefying ammonia and other various gases. His methods relied on a system of high pressures and low temperatures. This would soon prove to be a crucial part of the modern refrigeration system.
In 1834, the very first working vapor-compression refrigeration system was built. It was built by Jacob Perkins, an American living in Great Britain at the time. Even this very early refrigeration system was designed to operate around the clock. This was achieved through the use of a closed circuit compression system.
It wasn’t until 1856 that the first useful and practical refrigeration system was built in Australia by British native James Harrison. His system could use ether, ammonia, or alcohol. His machine was introduced to a dozen stores, meat houses, and breweries everywhere.
From 1859 through 1880, scientists everywhere worked to improve the refrigeration system. People were beginning to see the value and importance of the developing appliance.
Refrigerators weren’t found in homes until 1913, when Fred W. Wolf built the first residential refrigerator. These early appliances relied on a traditional icebox with a refrigeration unit mounted on top of the box. The basis for the Kelvinator was built during the following year in Detroit.
The Kelvinator was the first mass-produced refrigerator that featured automatic controls. Other people would continue to perfect the process of refrigeration and the design of the compact refrigeration system through the following century.
The General Electric refrigerator released in 1927 was the first to see widespread use throughout the entire country. The model was called the “monitor top” because it resembled a turret from an 1860’s warship.
The compressor was located above the box because of the great deal of heat it produced. More than 1 million units were produced and sold in America. The medium for refrigeration was sulfur dioxide, which was very harmful to humans. Another possible medium was methyl formate, which is also harmful.
Freon was finally introduced during the 20s and it helped take the market a step further in terms of safety, reliability, and maintenance. It was a safe alternative to the potentially harmful gases mentioned above.
During the 40s, the separation of the freezer and the refrigerator as separate units became commonplace. At the time, these freezers were called deep freezers. It wasn’t until after WWII that deep freezers were mass produced for American homes.
The 50s and 60s were full of technical and electrical advances that improved the refrigeration process. The automatic ice making and automatic defrosting mechanisms were invented during these times.
The invention and application of the refrigeration system also led to many other great advances in the world. For example, frozen foods became readily available to the public. This saved people time and money, while also allowing them to enjoy meals that might otherwise be out of season.
It’s really impossible to mention the refrigerator without mentioning the freezer. The two are basically one and the same with slight variations in temperature thresholds. Food is considered safe for much longer periods of time when kept at temperatures below 0°F. Most freezers work to around -9°F.
In units where the freezer and refrigerator are together, as with most modern refrigerators, both units rely on the same coolant loops to maintain appropriate temperatures. Thus, if the temperature is dropped too low in the freezer, then it will be difficult to maintain a high enough temperature in the refrigerator.
Some freezers come as separate units entirely. These freezers are capable of maintaining a lower temperature. Most modern freezers now come with thermostat displays and ice dispensers. Many of these new components can still be repaired or replaced quickly and cheaply.
How Refrigerators Work
At its core, a refrigerator is a very simple machine. Of course, there is some degree of mathematics and physics required to understand the real nature of what’s going on behind the scenes; however, it’s good to have a general idea of what is happening. It makes repairs much easier.
Most of today’s modern refrigerators use a closed vapor compression cycle. There is a refrigerant used that boils at a temperature much lower than water. For example, pure ammonia begins to boil around -27°F. That might seem like a cold temperature, but to ammonia it’s extremely hot.
Pure ammonia is very toxic and no modern refrigerators actually use this refrigerant anymore. Today’s refrigerators use much safer refrigerants.
The compression system relies on two opposing pressure systems. The first is the low pressure system, which is the evaporating refrigerant. The second is the high pressure system, which is the condensing refrigerant. The refrigerant moves in this cycle of pressure between the evaporator and the condenser.
The compressor is responsible for sucking the vapor from the evaporator and feeding it to the condenser. Heat is removed from gas inside of the condenser.
The amount of heat removed is the same as the amount of heat absorbed while in the evaporator, as well as the additional heat caused during compression. The gas is cooled and eventually returns to its liquid form.
Inside of the condenser, an external device is used to extract the heat. Some refrigerators used water cooled tubes. The cold water is pushed through the condensing coils and absorbs the heat.
The refrigerant itself leaves the coils through a special refrigerant liquid line. An alternative to the water-cooled system is the air-cooled system. An air cooled refrigerator is a lot like the fan cooling of computers.
Air-cooled systems are much easier to install, cheaper to install, and easier to repair. There’s also no risk of water getting too cold and freezing inside of tubes. The air is blown across the tubes and absorbs the heat. This causes the refrigerant to return to its liquid state inside of the coils.
Inside of these refrigerators there’s always a small tank which is usually black. This tank is there to store all of refrigerant liquid that is not currently circulating through the pressure systems. The tank must be large enough to hold all of refrigerant in the system at one time. A valve near the outlet is used to pump refrigerant into the tank.
The expansion valve works to maintain the needed differences in pressure. It can be thought of as a small, pin-sized tube that connects the condenser and the evaporator.
A thermostatic expansion valve is somewhat of a control mechanism. The overall temperature of the vapor that is exiting the evaporator will control the amount of flow allowed to exit the expansion valve.
The flow itself is monitored by a simple needle and diaphragm that is located inside of the valve. Three different forces work together on the valve: pressure from evaporation, superheating of the spring, and the pressure that is exerted by the thermal lamp.
While the lamp is at a higher temperature than the refrigerant, the valve will remain open and allow refrigerant to flow. When the difference in the temperatures of the bulb and the gas is smaller than the settings, the valve will close and restrict movement of refrigerant.
The main component of the refrigeration system on the low pressure side is the evaporator. This is where the liquid refrigerant enters and is turned into vapor. While the refrigerant is changing to a vapor, the heat is absorbed and used to freeze the eutectic solution.
One small component that may malfunction with time is the suction accumulator. This device is used in refrigeration systems to prevent the refrigerant from flooding backwards. The accumulator will trap the liquid before it can reach the compressor and cause damage. This component is located on the suction line between the evaporator and the compressor.
Probably the most likely component to fail inside of a refrigerator is the capacitor. Capacitors serve a few different functions, such as start assistance and DC voltage smoothing. Capacitors may eventually burst, leak, or overheat and require replacing.
In time, any and all of these components could fail. They are designed to last a long time, but nothing really lasts forever. It is possible to repair and replace some of them at home, but others will require a professional touch.
Troubleshooting and Repairs
When problems do occur, it’s nice to know what they actually are and what the source of the disruption is. Troubleshooting a refrigerator involves narrowing down all of the possible sources for a certain problem. This ensures the person fixing the fridge is actually fixing the right problem.
Professionals use tools, experience, and general know-how to troubleshoot most problems with refrigerators. The owners could actually do the same thing without the need to pay for a professional. Learning to troubleshoot will help them spot problems which they can fix themselves and problems that require more work or attention to detail.
The first step of troubleshooting is usually the problem. There is a long list of potential symptoms coming from a refrigerator in distress. There could be water leaking on the floor, the freezer side may not be freezing, or maybe it’s making a loud noise. Whatever the problem is, troubleshooting will help identify the cause and help develop a solution.
Following will be various symptoms and their potential causes. Owners should use this section to diagnose their refrigerator problems so they can move forward with the proper repairs as quickly and cheaply as possible.
Refrigerator Doesn’t Turn On or Cool
When the refrigerator doesn’t turn on at all, it can seem like an overwhelming disaster, especially if there’s food inside just waiting to go bad. Reacting quickly and calmly can potentially save whatever is inside of the refrigerator.
The very first step is to open the door and check for the inside light. If the light is coming on, but the rest of the refrigerator isn’t working, then it’s definitely an internal problem. However, if there’s no light and no refrigerator, then it’s possibly a problem outside of the refrigerator.
If this is the case, then the first thing to do is check and make sure the refrigerator is actually plugged into the wall. As funny as it sounds, this is the problem more often than not. If the refrigerator is plugged in and still not operating, then the problem is elsewhere.
The next step is to check the home’s circuit breaker. It is possible that the compressor inside of the refrigerator pulled too much current, thus causing the circuit break to trip or blowing a fuse. If the breaker is flipped, then it’s as easy as flipping it fully off and then back on. If the fuse is blown, then it will need to be replaced immediately.
If there is no blown fuse, no tripped circuit, but still no power, then it’s time to check the outlet. Checking the outlet properly requires a multimeter or voltmeter. Normal home voltage should range between 110 and 120 VAC. Those without a multimeter could simply try plugging another appliance into the same outlet to see if it functions.
If there is a proper voltage difference across the outlet, then the problem is most certainly with the refrigerator. The next step is checking the power cord on the refrigerator for any possible damage. The cord should be checked for possible cuts or breaks in the line. If an extension cord is being used, it should be removed entirely.
When the light inside of the refrigerator turns on, but the rest of the fridge isn’t operating properly, then it’s not a problem with the power source or the home. This usually means some problem with the coils, relays, timers, or settings. Step one is to check the temperature settings in the fridge.
Almost all refrigerators have adjustable temperature settings somewhere. These may be turned too high or too low. In older models, the settings are usually found on separate dials located at the top of the fridge and freezer on the inside. Newer models may use LED displays and touch buttons to allow for adjustment.
The ideal temperature setting for a refrigerator is between 37 and 40°F. The ideal temperature setting for a freezer is between 0 and 5°F. If the dial isn’t in this number range, then it should be adjusted. Give the fridge a couple of hours to adjust to the new temperature and check again to see if it is working properly.
It’s also important to make sure there is a significant amount of space between the back of the refrigerator and the wall. The same goes for the sides of the refrigerator. A minimum gap of three inches on each side is required to ensure proper airflow. There should be a one inch gap between the bottom and the floor. Without this space, the inside may not cool properly.
Condenser coils work inside the refrigerator to disperse heat created from the closed cycle of refrigerant. Over time, these coils can be covered in layers of dirt or debris. When this happens, the coils cannot sufficiently distribute the heat to the air around them. This means the vapor inside will not be able to get cool enough to condense to liquid form. This can cause a variety of problems, from a refrigerator that doesn’t cool properly to one that doesn’t turn on altogether.
Luckily, cleaning the condenser coils can stop this problem before it’s ever serious enough to ruin a perfectly working refrigerator. Before cleaning the coils, the owner should remember to unplug the refrigerator to avoid the potential of electrical shock.
The coils can be cleaned by vacuuming or by brushing the coils. Some coils may exhibit a filmy layer of buildup that can be cleaned away with some soap and water. It’s important not to splash excess water on any of the other electrical components of the refrigerator.
If the coils aren’t cleaned at least once a year, then they will work less efficiently, thus causing the appliance to work harder and consume more energy to cool down. Eventually, it may not cool down at all. If the coils are at floor level, then they should be cleaned at least twice every year. Most condenser coils are located on the back of the refrigerator and don’t require removing anything to access.
It may also be helpful to unplug the refrigerator for a few hours. After about two hours, plug the refrigerator back into the wall and listen for any noises. If it’s now running, but audibly, then it could be an internal problem causing the compressor to overheat.
It’s also possible for some of the individual components to fail. For example, the refrigerator may not be coming on because the temperature control is broken, even though it’s set on the appropriate temperature. These controls control the cooling system in the freezer and the airflow allowed into the refrigerator section. If they are broken, then the fridge and freezer may stop working entirely.
Testing the temperature control is fairly easy if it is a traditional dial or rotary style switch. After unplugging the refrigerator from the wall, remove the dial and the housing around the control. The dial should pull straight away, but the housing will be held by snaps or screws on either side.
Remove the metal housing from the hole. There should be two wires connected to either side of the dial. Label the wires in some fashion and then disconnect them from the temperature control switch. The connectors may be difficult to remove without the help of needle nose pliers. Always pull the connectors and not the actual wire itself.
Now is a good time to check the connectors and the terminals for any signs of corrosion or damage. Also check the wires that were connected to the housing. If any of these areas show signs of corrosion, then they need to be replaced immediately.
Properly testing the control itself will require a multimeter. Turn the control setting to off on the rotary switch and test the pair of terminals for continuity. If the control is in the off position, then the continuity reading should be near the high end of the scale. There should be no continuity. With the dial turned to the coldest setting, the reading should display a resistance of zero ohms.
If testing the temperature control does not deliver the results above, then the switch is faulty and needs to be replaced. Luckily, temperature control switches are not terribly expensive.
There are still more problems that may cause the refrigerator to not turn on or reach a cool temperature. The next potential source on the troubleshooting list is the evaporator fan. Inside all refrigerators are evaporator coils, and the evaporator fan is responsible for circulating the cool air produced by those coils.
Some refrigerators may have two evaporators working independently, but most often there is only one and it is located on the freezer side of the appliance. If the fan is not blowing, then cold air won’t be pushed from the freezer to the refrigerator. This may be why the freezer side is operating, but the refrigerator side is not.
Reaching the evaporator fan doesn’t require moving the refrigerator. It can be accessed by opening the freezer door after first unplugging it from the wall. It may be located behind the ice maker or a rear panel. Remove any screws or clips holding the rear panel in place and there should be a fan hiding behind it.
To test the evaporator fan for problems it is necessary to remove any additional screws that are securing the fan in position. This can be tedious work depending on the make and model of the refrigerator. Once the fan is removed, the fan can be pulled forward from the hole and properly tested.
Most fans are connected with two wires, but some fans will have a third wire. The wires should be labeled before being disconnected. Labeling the wires helps you remember where they go when reattaching the evaporator fan. Once again, pull the wires from the terminals at the point of the connectors.
The easiest test for the motor is to spin the fan blade manually. The fan blade should be able to rotate smoothly without problem. If the fan blade doesn’t move around smoothly, then it’s the motor that needs to be replaced.
The next test will require the use of a multimeter to check the continuity between the terminals on the motor. The ohms setting should be on x1 and one probe should be placed on each terminal. There should be a reading between 0 and 8 ohms on the terminals. The fan must be replaced if the resistance is higher. Like all other fans, they do wear down and stop working with time.
The evaporator fan isn’t the only fan motor working hard inside the refrigerator that can malfunction. Condenser fan motors may exhibit problems at times that cause the fridge to stop working properly. It may be something simply caught in the blade of the condenser motor.
The condenser fan works to pull cold air over the condenser coils on the back to keep them cool. If the fan stops functioning properly, then the coils can’t cool properly, nor can the rest of the refrigerator. The fan can be tested in the same fashion as the evaporator fan motor, but it is a little harder to reach.
Accessing the condenser fan usually requires moving the refrigerator away from the wall and removing the back access panel. Anyone performing this test should always unplug the refrigerator first to protect themselves from electrical shock.
The defrost timer may also malfunction in time, causing the refrigerator to stop cooling or to become covered in frost. This is because it causes the refrigerator to get stuck in a cycle of continual defrosting or continual refrigeration, when it must really move back and forth between both.
Older refrigerators worked on a constant schedule. Every six hours the refrigerator would stop sending power to the refrigeration cycle and start sending power to the defrost cycle. Newer models have improved the process by adjusting the defrost timer to only advance in time when the compressor or defrost cycle is actually running, rather than every six hours flat.
When the timer malfunctions, it will stop advancing in time, thus causing the fridge to become stuck in cooling mode or in defrost mode. Either way, the refrigerator won’t be functioning properly and the timer will need to be replaced.
Testing the timer isn’t difficult and can easily be performed at home, without the help of a professional. The timer itself is usually located directly behind the front grill, which is often referred to as the “toe kick”.
If the timer is not there, then it may be behind the cover plate that is located inside the refrigerator itself. It may also be found inside the temperature control console or on the back of the fridge near the compressor.
The next step is to manually turn the timer to test whether it is failing to advance on its own. This is simple. The person testing the timer needs to locate the advance screw and turn it in a clockwise motion until there is an audible click. This will mean that the timer has advanced and switched modes.
If the refrigerator was already cooling, then it should now be defrosting. If it was defrosting, then it should now be cooling. To see if it has now switched modes, leave the refrigerator and return in about 45 minutes. If the fridge is now cooling off then the switch is advancing properly. If it doesn’t advance, then the entire switch must be replaced due to a faulty timer motor.
If the timing does advance as it should when adjusted manually, then it’s time to break out the multimeter and test the switch further. The timer is typically held in place with only one or two screws that can be easily removed. It may take some rocking and pulling to free the timer from its hole. The timer can only be replaced the way it was removed, so there’s no need to label or mark connections.
The first step is the same continuity test that was performed on previous components. With ohms setting at x1, there should be continuity between the common terminal and all other terminals except one. The common terminal will have a label of “C” or “3” nearby on the switch.
Manually adjust the timer again until the click is heard and test the terminals once more. Now, a different pair of terminals should have no continuity and the other one or two should. This indicates that the timer has properly switched modes. If the continuity on the terminals doesn’t switch with the advance, then the problem is with the timer and it needs to be replaced.
Another component required for the refrigerator to turn on and cool properly is the start relay. This is a small device that is located near the side of the compressor on the back of the refrigerator. The relay may be located inside of a larger terminal box. Once again, safety first: unplug the refrigerator before attempting to test or examine these components.
A relay is a fairly straightforward electrical component. A smaller voltage, possibly 12 volts, across a pair of terminals causes an electrical current through a coil. This coil is then magnetized, which causes a metallic switch to close.
The 120 VAC from the outlet flows through this now closed switch. This causes the compressor to power on. Without the small voltage magnetizing the switch, the compressor cannot turn on and the refrigerator cannot function.
To test a relay, first look at all of the terminals for any signs of corrosion or damage. Terminals may need to be cleaned to allow electrical current to flow. If the terminals are in working condition, then it’s time to test for the next problem.
It’s important to note that there is one alternative to the coil relay and that is a solid state relay. Solid state relays utilize transistor technology instead of magnetic coils to control the flow of current. Unfortunately, these cannot be tested as easily as a magnetic relay.
A continuity test will work with the relay as well. There should be two terminals labeled “S” and “M” on the relay. There should be continuity between these two terminals. When turned upside down, the switch should open automatically, causing a reading of 0 ohms, or no continuity.
There should also be a third terminal, possibly labeled “L”. There should be continuity between “L” and “S” terminals and between the “L” and “M” terminals. When upside down, the relay should still have continuity between “L” and “M”, but not between the “L” and “S” terminals.
If the relay doesn’t pass all of the troubleshooting tests above, then it is the source of the problem and needs to be replaced. Replacement relays are very cheap and easy to find online. Replacing them is extremely easy.
Not only is there a start relay, but there is also a start capacitor. The capacitor is like a battery that depletes all of its charge at once to give the compressor the boost it needs to start. Capacitors are usually the first component in any electrical device to go bad or malfunction.
A capacitor used to start a motor is placed under even more stress than the average capacitor and can eventually fail for a few different reasons. Old age and too much heat are the top reasons for capacitor breakdown. If this happens, the refrigerator will refuse to start.
The first step is actually locating the start capacitor. It is usually located in close proximity to the compressor and the start relay. It will look a lot like a small can, possibly bare metal or black in color. There should be two or three terminals at the bottom with wires attached.
Expose the electrical connections at the bottom, but be careful not to touch them. Even if the refrigerator is unplugged from the wall, capacitors can still store enough electricity to be dangerous. The capacitors must be manually discharged and probed before handling.
The capacitor can be charged a few different ways. The most effective DIY method is to connect a high-watt power resistor between two screwdrivers. These resistors cost less than a $1 at most places where they are sold.
Once the rig is set up, it is important to touch one screwdriver to each terminal. The stored charge will slowly drain through the resistor as it flows between terminals. The screwdrivers must be held in place for several seconds.
After discharging, a multimeter set to test voltage should be used to test the two terminals. There should be 0V across the now-discharged capacitor. This means it’s now safe to touch and move.
The next step is to take a pair of needle nose pliers and carefully remove the connectors holding the wires to each terminal. Once the wires and connectors are removed, the capacitor should easily come away from the refrigerator for proper testing.
The side of the capacitor should state its appropriate voltage levels and capacitance. An average start capacitor is rated 110V and around 185mfd, or Microfarads. Now it’s time to test the capacitor with a digital multimeter to see if its capacitance is still at the appropriate level.
A capacitor that is functioning properly should read within 5% of the capacitance labeled on the side. If it is not within this range, then the capacitor has been damaged and needs to be replaced before the refrigerator will start again.
If the capacitor is functioning properly, then it could be the overload protector preventing the refrigerator from starting. The overload protector is a small, circular device that is usually located in the box with the start relay.
Removing the overload protector is very simple and testing it for continuity between its two terminals is straightforward. If there is no continuity, then the overload protector is damaged and needs to be replaced.
The purpose of this component is to protect the sensitive compressor motor from potential electrical damage. Without the overload protector functioning, no power can flow to the start relay or the compressor, thus preventing the refrigerator from starting.
If the refrigerator is still not turning on at all, aside from the inside light, then the final component to test is the compressor motor itself. The compressor applies a strong mechanical force to the refrigerant in its gas form.
The gas is then pushed through the coils and radiates heat before passing through the expansion valve located in the freezer. There, it changes back to a low pressure state and carries heat out of the freezer back through the cycle.
Most refrigerator compressors can be accessed from behind the refrigerator in the bottom section. The terminal box containing the start relay and overload protector should be located directly beside the compressor.
As always, these components should not be handled unless the refrigerator has been unplugged from the walls.
First remove the terminal box and the compressor relay. This should reveal the terminals for the compressor motor. It is entirely possible to test the motor without removing the compressor from the refrigerator.
The motor can be tested in continuity mode with x1 ohm settings. The person testing the motor should place one probe on one terminal and then another probe on any of the remaining terminals. There should be continuity between these terminals.
As a matter of fact, there should be continuity between all of the terminals attached to the motor. If there is no continuity, it could be a wire has burned or the motor is damaged internally.
Repairing or replacing a compressor is not an easy job. This is one of those few repairs that are best left to a professional. It’s often easier to replace the refrigerator entirely than to replace the compressor, but that all depends on the make and model of the fridge.
Refrigerator Works, But Light Does Not
If things are in reverse and the refrigerator is working, but the light isn’t coming on, then there are far fewer components to worry about. The probably is usually one of two things and the solutions are easy.
The first step is to replace the bulb. Replacement bulbs can be found at most hardware stores and are pretty inexpensive. If replacing the bulb doesn’t work, then the problem is located in the door switch.
The door switch controls the interior light of the refrigerator. It can also control the internal fan in some refrigerators as well. If the door is closed, then the switch is opened and the light goes off. When the door is opened, the switch closes and the light will come on instead.
When the door switch stops working, the light may stay on or off all of the time. If it’s always off, then it’s annoying, but if it’s always on, then it can heat up the refrigerator too much to maintain proper temperature settings.
The refrigerator should be unplugged before locating and removing the door switch. The switch is usually located on the inside of the refrigerator along the frame of the door. There may be a retaining screw to remove.
If the switch won’t come off easily, it may take a putty knife covered with masking tape at the end. The putty knife works well for prying beneath the edges of the switch and pulling it from its hole in the refrigerator. It should be pulled gently to prevent the wires from disconnecting.
Most switches are connected to only two wires. However, if the switch controls additional components, then there may be more wires attached. Label the wires and then remove them from the switch using a pair of needle nose pliers.
Inspect the wire connectors and terminals of the switch for corrosion or debris. If needed, clean the terminals to expose the metal. If the connectors have been corroded severely, then they must be replaced to establish a proper electrical connection.
If the problem isn’t the connectors or terminals, then it is within the switch itself. Using a multimeter to check for continuity on x1 ohms will reveal if this is the case.
The multimeter should show continuity while the switch is open, but when pressed it should read no continuity, or infinity ohms. If the switch does not work in this manner when tested then it needs to be replaced.
Freezer or Refrigerator Isn’t Cool Enough
If the refrigerator turns on, but won’t get cool enough, then it could be a few different problems. Temperature controls, condenser coils, evaporator fans, and defrost timers have all been covered already and are all potential sources of the problem. However, there are a few more possibilities that have not yet been covered.
The first possible source of the problem is a lack of sufficient airflow. The evaporator fan works by blowing cold air off the pipes and into the freezer. The air flows through the freezer and then a portion of that air travels into the refrigerator to keep it cool as well.
Most temperature controls for the refrigerator side simply control the amount of cold air allowed to flow from the freezer to the fridge. If the temperature is turned down, then more air should flow into the refrigerator. At times, the vents between the refrigerator and the freezer may become blocked.
Dirt, food, debris, and ice can all pose a potential problem to the airflow inside of the refrigerator. Owners can work to avoid this problem by regularly checking their vents and ensuring there is no blockage.
If the vents get blocked, then the refrigerator cannot cool. They may also get stuck open, which will cause the refrigerator to get too cold and possibly freeze.
Checking the vents is mainly a visual process. Unplug the refrigerator and take a look at the inside vents. They should be easy to locate because they are located on the connecting panel of the fridge and freezer. The cause may be too much clutter in the fridge or freezer rather than anything inside the vent itself.
If the problem is a visible buildup of debris, then the vents will need to be cleaned. If it is ice blocking the vent, then it is possible to clean using a hair dryer. Set the hair dryer on low and blow the ice that is blocking the fan. Ensure no ice melts inside of the hairdryer.
The vent may be located directly beneath the temperature control module. There should be a housing surrounding the vent that snaps away, but it may also be held with screws. There may also be an additional vent control that must be removed before accessing the vent.
If the freezer is on top of the fridge, instead of beside it, then it may require removing the freezer floor to properly inspect for anything that doesn’t belong. It’s much easier to check when the freezer and refrigerator are built side-by-side. There’s rarely ever a need to replace the vent.
Probably one of the most common causes of insufficient temperatures inside the refrigerator or freezer is a faulty door seal. There is a flexible, rubber seal that goes along the edges of all refrigerator and freezer doors. These seals prevent the warm air from entering the refrigerator.
When closing a refrigerator door, the rubber seal should make perfect contact with the frame all the way around the door. If there are any deformities along the way, then it’s likely that warm air is making its way inside and causing the temperature to drop.
Over time, a faulty seal can lead to more serious problems, such as compressor malfunctioning. The refrigerator will try to work harder to maintain the proper temperature, but if it is unable then it will damage internal components.
Testing the seal for continuity is very simple. A dollar bill should be inserted between the seal on the door and the refrigerator itself, then the door is closed over the dollar bill. When pulling the bill from between the seal and refrigerator there should be a noticeable amount of tension on the paper.
If the bill comes out easily and without tension, then the seal is faulty and will need to be removed and replaced as soon as possible. In some cases, it’s possible to realign the door seal without replacing it entirely. The seal should also be cleaned occasionally to help maintain full flexibility.
Another possible problem is the defrost heater. If the refrigerator has the freezer on top, then the heater is located under the freezer floor. If the refrigerator and freezer are side-by-side, then the heater is usually located at the back of the freezer.
To test the heater, the first step is to remove everything in the freezer and locate the back panel. Once the panel is located, there is likely a few screws or clips to remove that are holding it in place.
Working with a freezer-on-top model is slightly more difficult. It may require removing plastic molding to remove the freezer floor and access the defrost heater. The molding should be removed slowly and carefully without force. It’s also helpful to first warm it with a hot towel.
Once the panel is removed, the revealed heating element will be one of three different varieties. It could be a simple, exposed metal rod; a metal rod that has been covered with a coil; or a coiled wire sealed inside of a glass tube. Regardless of the type of heating element, all three are tested the same.
Every heating element has terminals for two connections. One wire has electrical current going in and the other coming out. As it passes through the element, the resistance resists the flow of the current and the work it takes the electricity to pass through is released as heat.
Use the needle nose pliers to remove the wires connected to the heating element. Always pull the wires from the connecting portion to prevent damaging or breaking the wires. As usual, check the terminals for corrosion, wear, or breakage.
The next step is to take out the multimeter and turn it to continuity mode. With the ohm setting at x1 the reading could be several possible numbers. As a heating element does have resistance, the reading should never be 0 ohms.
It should also never be infinity because that would mean no electricity could pass. If it is either of those numbers, than the element is damaged and needs replacing. However, it’s impossible to list the exact number it should be because all heating elements are different.
The best method for testing the element properly is finding a manual or schematic that contains information for that exact heating element. Use the schematic and compare the results from the multimeter. There’s also a chance the element has the resistance labeled.
Some newer refrigerators rely on a thermistor to detect the temperature in the refrigerator and control certain settings. The thermistor is just a variable resistor with resistance changes in accordance with the temperature. It’s often also referred to as a temperature sensor.
Thermistors can be found in freezer-on-top and side-by-side refrigerators, but it isn’t found in all of them, especially older models. The thermistor is read and monitored by the main control panel. Some refrigerators have more than one thermistor.
Testing these sensors requires a multimeter with resistance testing capabilities. Remove one or both thermistors and label the wires to remember their correct position.
The sensors need some time to warm up to room temperature before testing. Once they’ve had a bit of time sitting on the table, test the ends of the leads with an ohmmeter or multimeter. At 72°F, the multimeter should read close to 6.2k ohms, but it could be different with different models.
The important thing is that the sensor doesn’t read 0 ohms or infinity ohms, which would mean the thermistor no longer works and must be replaced.
If all of the previous possibilities have been ruled out, then there is a slight chance the problem lies with the main temperature control board. This board monitors thermistors and controls output voltage sent to fans, motors, and compressors.
The job of the temperature control board is just as the name implies: controlling the temperature in the refrigerator and freezer. Testing individual components on the board is extremely tricky and requires knowledge of electronics and circuitry. It’s always easier to have this looked at by a professional or replaced entirely if all other solutions have failed.
One final possibility is a refrigerant leak. Leaks are extremely uncommon because refrigeration systems are designed to last a long time. However, especially in systems using water cooling, it is possible for pipes to freeze and burst.
When a pipe bursts and refrigerant leaks, the freezer or fridge will become impossible to keep cool. Refrigerant never requires refilling, unlike other items that use the liquid, such as air automobiles. Refrigerators are designed with a closed circuit that constantly uses the same refrigerant time and time again.
A refrigerant leak isn’t only bad for the refrigerator, but it can also be bad for the food and the owner. Refrigerant is never safe for humans, especially if inhaled in its vapor form. The best method for repairing the leak is contacting a professional. The potential health risks make it too dangerous for the average DIYer.
It’s for this reason people should never chip away at ice that has built up inside of their freezer. Chipping away could potentially break open the pipes containing the refrigerant gas, thus causing a leak and insufficient cooling in the unit.
How to Repair a Noisy Refrigerator
A noisy refrigerator can turn a peaceful night into a complete nightmare. There are a few motors and other moving parts on a refrigerator that are responsible for the bulk of the noise heard. However, sometimes the refrigerator is making more noise than it should. This could be the sign of a real problem.
Troubleshooting a noisy refrigerator requires decent hearing capabilities. The best first step to take is attempting to locate the exact area the noise is coming from. Pinpointing the location lets you know what component or components are the most likely source of the noise.
If the noise is coming from the bottom of the refrigerator, then it could be coming from the compressor or the condenser fan motor. Problems with the condenser fan motor could also cause the refrigerator to maintain lower temperatures than normal. If the refrigerator isn’t staying as cool as normal and noises are coming from the bottom, then it’s a good sign that there’s a problem with the condenser fan.
Inspecting the condenser fan is easy. The refrigerator should be unplugged and then moved away from the wall. A rear access panel will block access to the condenser fan and many other important components.
The fan should be clearly visible once the panel is removed. If there is any debris, food, or ice in the fan, then it is the likely source of the noise. It’s important to keep this area clear of debris, but it does get dirty fairly regularly.
Owners are advised to take a vacuum and clean the fan, as well as any other debris behind the access panel, on a regular basis. This will help lower the noise level and ensure the refrigerator is operating as it should.
If the noise is coming from the freezer, rather than the bottom, then it’s more likely a problem related to the evaporator fan motor. This motor is located directly behind an access panel inside the freeze. It pulls air over the coils while the compressor operates.
A problem with this motor could also lead to insufficient temperature levels in the freezer. Once the refrigerator is unplugged, inspecting the evaporator motor is easy.
Items and shelves in the freezer blocking the panel must first be removed. There may also be screws holding the panel in place. Once the panel is removed, the owner needs to inspect the blade for debris, ice, or food.
The blade may have come loose. A loose blade can cause a lot of unwanted noise on a fan. It may also be ice on the blade that is causing the noise.
The ice can be removed with a hair dryer set to “low” heat. Leaving the refrigerator unplugged for a day could also help, but that’s usually out of the question if there’s food being stored inside.
A grommet is used to isolate the evaporate fan motor from the freezer bracket. It is meant to reduce the noise caused from the constant vibration. This grommet can wear down with time and requires replacing.
If the fan is operating fine and there are no obstructions, then replacing the grommet is the likely next option. Many people have noticed a significant reduction in noise from their freezers once they’ve replaced their old grommet.
One last reason a refrigerator might cause noise is because it is not level. A refrigerator needs to remain level for a few different reasons. If it is not leveled properly, then doors may stay open and pipes may not drain properly.
When drainage is obstructed it could cause unusual temperature fluctuations inside the refrigerator, leading to ice obstructing the evaporator fan. Refrigerators were designed with the idea that they would be operated on a level surface at all times.
The Refrigerator Is Leaking!
There is a lot of water and ice moving around inside of a refrigerator and freezer, but nobody ever wants to see that water where it shouldn’t be. When there’s a leak, whether it’s inside the refrigerator or outside of the refrigerator, it needs to be fixed fast.
Luckily, most the problems that cause leaks aren’t very serious and can be fixed fairly quickly. Step one is identifying whether the leak is on the inside or the outside of the refrigerator. If it is on the outside, it may still be leaking inside and draining out through a faulty seal.
If the water is leaking inside of the refrigerator, then the first possibility is a problem with the drain tube. The drain tube comes from inside the refrigerator and leads to the drain pan on the outside.
If the refrigerator isn’t cleaned of debris and food properly, it is possible for the drain pipe to become clogged. When the refrigerator can’t drain properly, the water will begin to back up until it sitting inside of the unit itself.
There is also a drain pipe inside the freezer. When that pipe is clogged the water backs into the freezer and is frozen as ice on the freezer floor. If there is a buildup of ice and frost on the floor of the freezer, then clogged drain tubes are a potential cause.
The first step is to unplug the refrigerator from the outlet to ensure there is no power going to the unit. The drain tube is usually located near the bottom of the refrigerator on the inside. It may be directly beneath the vegetable crisper or in the wall itself.
The drain can then be cleaned by pouring a combination of bleach and water into the drain. It’s usually easier to force the solution using a baking syringe. Sometimes, the syringe is not enough to force the liquid through the drain tube.
If the clog is too much for the liquid, then a piece of quarter-inch flexible tubing should do the trick. Start from inside the refrigerator and slowly push the flexible tubing through the drain tube, pushing the clog out into the external drain pan.
Water inside the refrigerator may also come from a refrigerator that is not level. An imbalance can cause water to leak from the ice maker into other parts of the freezer or refrigerator.
When the water is leaking outside of the refrigerator rather than inside, then the problem is more likely the drain pan instead of the drain tube. This pan is located on the bottom the refrigerator, directly behind the grill at the front.
Accessing the pan is very simple. Just remove the front grill and pull the drain pan with both hands. It should come free without removing any additional screws.
The drain pan is one of those components in the refrigerator that needs some regular care and maintenance. The pan should be cleaned at least once a year. Neglecting the cleaning of the pan can lead unwanted noises or leaking beneath the refrigerator.
Properly Maintaining a Refrigerator
Most of the problems mentioned in this book can be avoided through some scheduled TLC. Refrigerators are designed to last a long time, but they can’t make it that long without some help from the people who own them. Cleaning and maintaining a refrigerator isn’t a lot of work, but really pays off in the long run.
Here are a few simple guidelines for extending the lifespan of any refrigerator and ensuring it runs efficiently at all times.
1. Keep the Temperature Settings Correct
It might seem like a good idea to turn down the temperature to freeze that ice cream a little faster, but freezers and refrigerators are designed to run in a specific temperature range.
Temperature dials give owners complete control over the temperature of the freezer and sometimes the refrigerator, but keeping them in the designated range will keep the cycle running smoothly on the inside. For the freezer, it’s recommended to run between 0 and 5°F. The refrigerator is designed to operate between 37 and 40°F.
The temperature in the refrigerator is actually controlled through the freezer. If the temperature in the freezer is set too low, then it can impact the temperature in the refrigerator. This happens even if the refrigerator temperature dial is set to the appropriate temperature.
Air is blown from the freezer into the refrigerator through a vent. When the air is flowing in the proper temperature range, the refrigerator will naturally adjust to the designated temperature setting easier. If the freezer is set too low, then ice may appear in the refrigerator itself.
2. Keep Some Food in the Fridge
Keeping food in the refrigerator actually helps it run better. Refrigerators need some additional source of thermal mass to help them maintain an overall low temperature. The cool food helps absorb much of the warm air that rushes in when the door is opened. This allows the temperature to remain relatively unchanged.
3. Clean the Coils
Both sets of coils, the evaporator coils and the condenser coils, need some regular cleaning to run at peak efficiency. The coils are used to absorb heat and exchange heat. The coils need to be cleaned once or twice a year depending on their location.
Coils located on the back of the refrigerator can be cleaned at least once a year. These coils are large and easy to clean. A vacuum and a towel will usually do the trick. If these coils aren’t cleaned, then heat will stay trapped and the refrigerator won’t operate properly.
If the coils are on the bottom of the refrigerator, then they should be cleaned at least twice a year. More dirt and debris tends to build up beneath the refrigerator. Cleaning these coils is simple using the brush attachment on any standard vacuum cleaner.
4. Examine the Door Seals
The door seals are very important for keeping warm air outside of the refrigerator. If the seals are broken or damaged, then the fridge must work harder to maintain a constant low temperature.
When a refrigerator works harder it consumes more energy. That means more money for whoever owns the fridge. It’s much easier and cheaper to just fix the seals than it is to pay an extremely high electric bill.
The seals should also be cleaned at least once or twice a year. Cleaning them requires a tool with a small brush, possibly even a toothbrush if nothing else is available. A solution of water mixed with baking soda is enough to remove most dirt and grime.
A single dollar bill or piece of paper is enough to test if the seal is functioning properly. Close the paper between the seal and the refrigerator and slowly pull the paper away. If the paper comes free without any resistance, then the seals are damaged and may need to be replaced.
If the paper came free, but with some tension, then the seal is fine in that area. However, this test should be duplicated at multiple points along the seal to guarantee it’s working properly everywhere.
5. Clean the Fans
There are two important fans, the condenser fan and the evaporator fan. In time, these fans can become subject to food particles, frost, and various debris. Cleaning these fans at least once a year will reduce the noise coming from the refrigerator.
If the fans aren’t cleaned, then the inside temperature of the refrigerator may steadily rise. The fans help transfer heat and keep pipes cool, but are often neglected until it is too late. Some annual cleaning with a vacuum will prevent a lot of potential problems and repairs.
Conclusion
Refrigerators and freezers are marvelous machines. They have passed through centuries of trial and error, research and development, success and failure. The modern refrigerator of today isn’t a far cry from the models of the 19th century.
Take away the bells, whistles, touch pads, and television screens and the refrigerator is still the same machine it has always been. A few new components have been added for safety, regulation, or improved importance, but none that really changed the basic operation of the refrigerator.
How to Repair Refrigerators Quickly and Cheaply
Luckily, most of the components that can malfunction inside of a refrigerator are easy to replace and extremely cheap. The most expensive component is usually the compressor, but those almost never stop working.
There are quite a few small components, sensors, knobs, and dials in every refrigerator. More modern fridges tend to have more of these components and thus more things that can eventually go wrong.
Repairing a refrigerator cheaply is simple because the components are usually cheap. The only option that isn’t cheap is calling a professional to repair the fridge.
However, repairing the refrigerator quickly requires a different set of skills. First, the repairer must be prepared with the needed tools. No matter what the problem, there are a few tools that will make any repair easier.
The multimeter is likely the most important tool when it comes to testing and troubleshooting any component inside the refrigerator. It’s really the best tool when it comes to troubleshooting any component that runs on electricity.
Making quick repairs also requires the ability to quickly diagnose problems and determine what’s causing the malfunction. Once the problem is located, it’s usually as simple as removing the broken piece and replacing it.
The hardest part of repairing any refrigerator may be finding the right replacement components. Depending on the make and model of the fridge, the components may be available at the local hardware store.
It’s always easiest to use the Internet and find the components online. The website of the manufacturer for the refrigerator usually sells the needed replacement components or will lead to a supplier who does.
Taking Care of the Refrigerator
The final topic covered in the book was refrigerator maintenance. A few different points were covered, but there is still more when it comes to caring for a fridge. Locate the problem areas and remember to keep cleaning on a regular basis.
If regular care is provided to the refrigerator, then repairs may never be needed. Keep food from blocking fans and vents. Remove food as it ages and clean food off the refrigerator floor so that it doesn’t find its way into the drain tube.
Unfortunately, a time may come when it’s cheaper and smarter to just replace the refrigerator entirely. This is usually a last resort, possibly because it’s aged so much the manufacturer no longer sells replacement parts.
However, 99 percent of all refrigerator problems can be repaired quickly and cheaply at home.